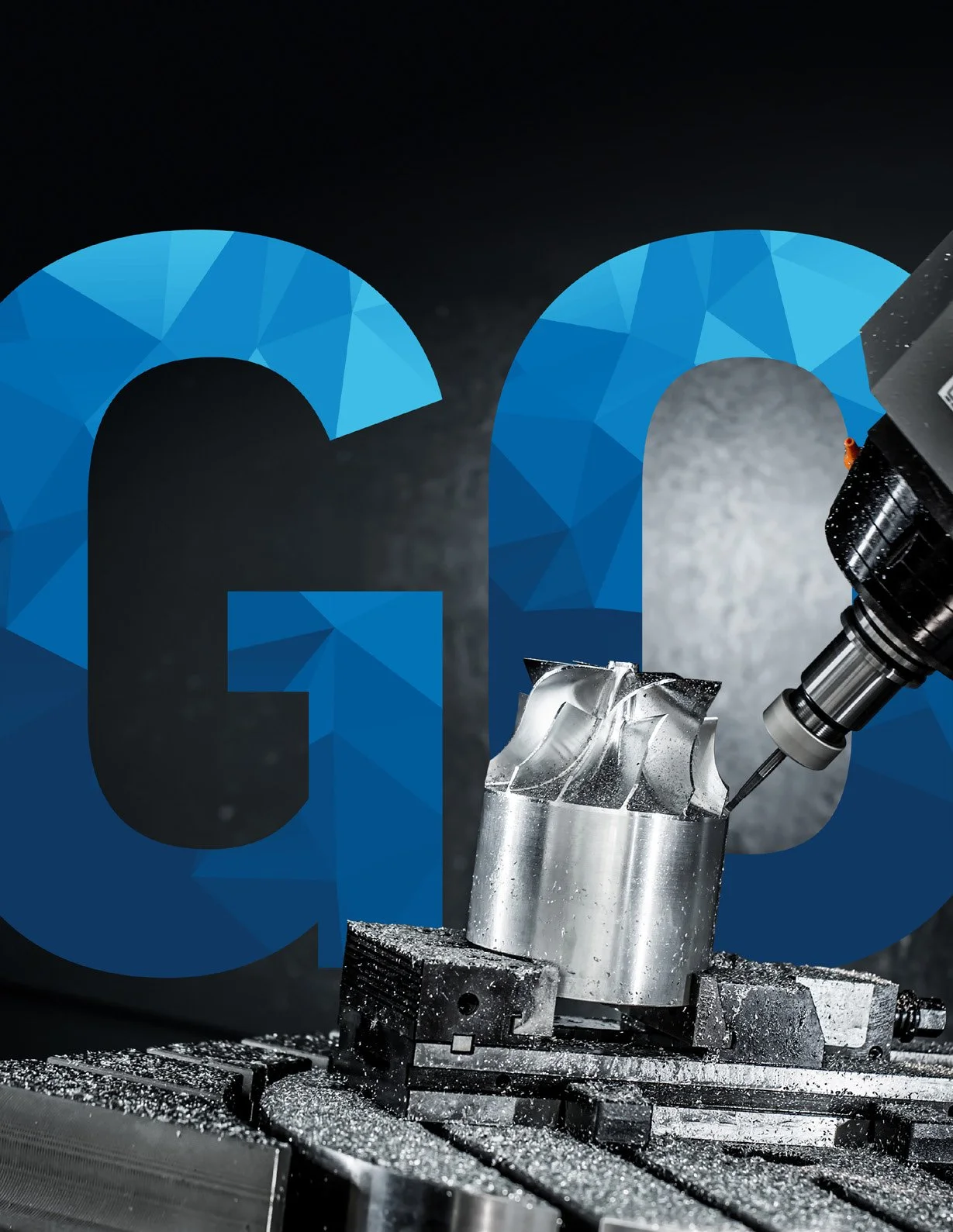
On-Demand Training
We were just like you when we started—nervous about CNC programming, but constantly curious. Now with decades of experience, we’re here to help you start your own GibbsCAM journey.
-
-
Lesson #1: 2D Creation
Make dough from scratch and learn to be creative with your sauce and toppings.
Make dough from scratch and learn to be creative with your sauce and toppings.
-
Lesson #2: 2D Creation (continued)
Ensure you have successfully completed Lesson #1 before proceeding with the above 2nd lesson.
Ensure you have successfully completed Lesson #1 before proceeding with the above 2nd lesson.
-
Lesson #3: Creating Workgroups
Workgroups in are layers used to separate different groups of geometry, including custom stock. One or more workgroups may be viewed at a time, however there may only be one active workgroup.
The viewing, selection and creation of workgroups is accomplished with the Workgroup list. Workgroup information and selection can also be performed through the Workgroup dialog, accessed from the Main palette.
Workgroups in are layers used to separate different groups of geometry, including custom stock. One or more workgroups may be viewed at a time, however there may only be one active workgroup.
The viewing, selection and creation of workgroups is accomplished with the Workgroup list. Workgroup information and selection can also be performed through the Workgroup dialog, accessed from the Main palette.
-
Text.
-
Lesson #5: Dimensioning 2D
The Dimensioning tool gives the ability to place text and show part dimensions. Dimension values are calculated from the current CS and visible based on the current workgroup. Any part of the dimension line, (line, arrowheads or text) may be dragged to reposition the dimension. Selection mode is active while the Dimensions palette is active.
The Dimensioning tool gives the ability to place text and show part dimensions. Dimension values are calculated from the current CS and visible based on the current workgroup. Any part of the dimension line, (line, arrowheads or text) may be dragged to reposition the dimension. Selection mode is active while the Dimensions palette is active.
-
Text.
-
Text.
-
-
-
Lesson #1: Solid Modeling Palette
Learn how to get your @gibbscam part correctly set-up and ready for programming on your live-tooled (mill/turn) lathe.
Learn how to get your @gibbscam part correctly set-up and ready for programming on your live-tooled (mill/turn) lathe.
-
Text.
-
Text.
-
Text.
-
Text.
-
Text.
-
Text.
-
Text.
-
Text.
-
Text.
-
-
-
Live-Tooled Lathe (Mill/Turn)
Learn how to get your @gibbscam part correctly set-up and ready for programming on your live-tooled (mill/turn) lathe.
Learn how to get your @gibbscam part correctly set-up and ready for programming on your live-tooled (mill/turn) lathe.
-
5-Axis Vertical Machining Center
Learn how to get your @gibbscam part correctly set-up and ready for programming on your 5-Axis VMC (vertical machining center).
Learn how to get your @gibbscam part correctly set-up and ready for programming on your 5-Axis VMC (vertical machining center).
-
3-Axis Vertical Mill
Learn how to get your @gibbscam part correctly set-up and ready for programming on your 3-Axis VMC (vertical machining center).
Learn how to get your @gibbscam part correctly set-up and ready for programming on your 3-Axis VMC (vertical machining center).
-
4-Axis Horizontal Mill
Learn how to get your @gibbscam part correctly set-up and ready for programming on your 4-Axis HMC (horizontal machining center).
Learn how to get your @gibbscam part correctly set-up and ready for programming on your 4-Axis HMC (horizontal machining center).
-
Multi-Task Lathe (MTM)
Learn how to get your GibbsCAM part correctly set-up and ready for programming on your multi-task (MTM) lathe.
Learn how to get your GibbsCAM part correctly set-up and ready for programming on your multi-task (MTM) lathe.
-
4-Axis Vertical Mill
Learn how to get your GibbsCAM part correctly set-up and ready for programming on your 4-Axis VMC (vertical machining center).
Learn how to get your GibbsCAM part correctly set-up and ready for programming on your 4-Axis VMC (vertical machining center).
-
-
-
Lesson #2: Align CS to Plane
Learn how to change the planar orientation of the current coordinate system. It can be used with geometry selected or no geometry selected.
The Align CS button will produce different results depending on what geometry is selected. Some groups of geometry will be used to define a plane, others will be used to define a normal vector for a plane. Defining a normal vector is equivalent to defining the depth axis.
Learn how to change the planar orientation of the current coordinate system. It can be used with geometry selected or no geometry selected.
The Align CS button will produce different results depending on what geometry is selected. Some groups of geometry will be used to define a plane, others will be used to define a normal vector for a plane. Defining a normal vector is equivalent to defining the depth axis.
-
4-Axis Vertical Mill
Learn how to create and work with multiple planes or coordinate systems for your 4-Axis VMC.
A Coordinate System is a plane in 3D space, with an origin and three axes. The origin is the point at which the axes intersect and serves as a zero reference point. The three axes are the horizontal, vertical and depth axes.
Learn how to create and work with multiple planes or coordinate systems for your 4-Axis VMC.
A Coordinate System is a plane in 3D space, with an origin and three axes. The origin is the point at which the axes intersect and serves as a zero reference point. The three axes are the horizontal, vertical and depth axes.
-
Horizontal Machining Center
Learn how to create and work with multiple planes or coordinate systems for your Horizontal Machining Center (HMC).
A Coordinate System is a plane in 3D space, with an origin and three axes. The origin is the point at which the axes intersect and serves as a zero-reference point. The three axes are the horizontal, vertical and depth axes.
Learn how to create and work with multiple planes or coordinate systems for your Horizontal Machining Center (HMC).
A Coordinate System is a plane in 3D space, with an origin and three axes. The origin is the point at which the axes intersect and serves as a zero-reference point. The three axes are the horizontal, vertical and depth axes.
-
Vertical Mill w/ Trunnion
Learn how to create and work with multiple planes or coordinate systems for your Vertical Mill with a Trunnion installed.
A Coordinate System is a plane in 3D space, with an origin and three axes. The origin is the point at which the axes intersect and serves as a zero-reference point. The three axes are the horizontal, vertical and depth axes.
Learn how to create and work with multiple planes or coordinate systems for your Vertical Mill with a Trunnion installed.
A Coordinate System is a plane in 3D space, with an origin and three axes. The origin is the point at which the axes intersect and serves as a zero-reference point. The three axes are the horizontal, vertical and depth axes.
-
5-Axis Vertical Machining Center
Learn how to create and work with multiple planes or coordinate systems for your 5-Axis VMC.
A Coordinate System is a plane in 3D space, with an origin and three axes. The origin is the point at which the axes intersect and serves as a zero-reference point. The three axes are the horizontal, vertical and depth axes.
Learn how to create and work with multiple planes or coordinate systems for your 5-Axis VMC.
A Coordinate System is a plane in 3D space, with an origin and three axes. The origin is the point at which the axes intersect and serves as a zero-reference point. The three axes are the horizontal, vertical and depth axes.
-
Live-Tooled Lathe (Mill/Turn)
Learn how to create and work with multiple planes or coordinate systems for your Live-Tooled Lathe (Mill/Turn).
A Coordinate System is a plane in 3D space, with an origin and three axes. The origin is the point at which the axes intersect and serves as a zero reference point. The three axes are the horizontal, vertical and depth axes.
Learn how to create and work with multiple planes or coordinate systems for your Live-Tooled Lathe (Mill/Turn).
A Coordinate System is a plane in 3D space, with an origin and three axes. The origin is the point at which the axes intersect and serves as a zero reference point. The three axes are the horizontal, vertical and depth axes.
-
B-Axis Mill/Turn
Learn how to create and work with multiple planes or coordinate systems for your B-Axis Mill/Turn.
A Coordinate System is a plane in 3D space, with an origin and three axes. The origin is the point at which the axes intersect and serves as a zero-reference point. The three axes are the horizontal, vertical and depth axes.
Learn how to create and work with multiple planes or coordinate systems for your B-Axis Mill/Turn.
A Coordinate System is a plane in 3D space, with an origin and three axes. The origin is the point at which the axes intersect and serves as a zero-reference point. The three axes are the horizontal, vertical and depth axes.
-
Multi-Task & Swiss Machining (MTM)
All MTM systems will have at least one coordinate system per spindle. These coordinate systems represent the primary planes on which a part can be machined.
Some of the various combinations of default Coordinate Systems follows. The actual coordinate systems you have available may differ, depending upon your machine configuration. 4 planes per spindle, the ZX, XY front face, XY back face and YZ.
All MTM systems will have at least one coordinate system per spindle. These coordinate systems represent the primary planes on which a part can be machined.
Some of the various combinations of default Coordinate Systems follows. The actual coordinate systems you have available may differ, depending upon your machine configuration. 4 planes per spindle, the ZX, XY front face, XY back face and YZ.
-
-
-
Lesson #1: Creating Tools
Learn how to select & define the tools that you want to use for machining processes using tool tiles in the Tools List. The Tool dialog defines the specific type, shape and material of a tool as well as how the machine uses and stores data for that tool.
Learn how to select & define the tools that you want to use for machining processes using tool tiles in the Tools List. The Tool dialog defines the specific type, shape and material of a tool as well as how the machine uses and stores data for that tool.
-
Lesson #2: Holes
The Holes process is used to drill, tap, or counter-bore selected points, circles or hole features and it can be used to drill entry holes for other processes. When the Drilling Function tile is combined with a Tool tile, the Holes Process dialog will appear on the screen.
The Holes process is used to drill, tap, or counter-bore selected points, circles or hole features and it can be used to drill entry holes for other processes. When the Drilling Function tile is combined with a Tool tile, the Holes Process dialog will appear on the screen.
-
Lesson #3: DoIt vs. ReDo
Defining when it is appropriate to select "DoIt" for an operation, versus "ReDo" for an operation, and the consequences of each selection.
Defining when it is appropriate to select "DoIt" for an operation, versus "ReDo" for an operation, and the consequences of each selection.
-
Lesson #4: Machining Markers
Machining Markers appear on selected geometry for contouring processes in order to designate the cut shape. To move a marker, place the cursor over the marker and click and hold down the mouse button. The cursor changes to the marker. This is called “picking up a marker.” You can then move the marker to the desired location and drop it by releasing the mouse button.
Machining Markers appear on selected geometry for contouring processes in order to designate the cut shape. To move a marker, place the cursor over the marker and click and hold down the mouse button. The cursor changes to the marker. This is called “picking up a marker.” You can then move the marker to the desired location and drop it by releasing the mouse button.
-
Lesson #5: Contouring
The contouring process is used to make passes along a shape or multiple shapes. The toolpath can be set to either side of the geometry or on center. When multiple shapes are selected the toolpath is automatically on center, which is typically used for engraving.
The contouring process is used to make passes along a shape or multiple shapes. The toolpath can be set to either side of the geometry or on center. When multiple shapes are selected the toolpath is automatically on center, which is typically used for engraving.
-
Lesson #6: Face Milling
Face Milling completely automates clearing material from the face of a part. When Face Milling is selected, the bottom portion of the Roughing dialog changes.
Face Milling completely automates clearing material from the face of a part. When Face Milling is selected, the bottom portion of the Roughing dialog changes.
-
Lesson #7: Roughing Offset Pocketing
Offset processes are the standard pocketing operations with concentric toolpath.
Offset processes are the standard pocketing operations with concentric toolpath.
-
Lesson #8: Offset Pocketing with Cleanup
Offset with Cleanup processes create an Offset toolpath with the corners extended to clean areas that didn’t receive much of the tool in the first pass.
Offset with Cleanup processes create an Offset toolpath with the corners extended to clean areas that didn’t receive much of the tool in the first pass.
-
Lesson #9: Zig Zag Roughing
The Zig Zag roughing option creates straight lines at a specified angle and contour moves at the boundaries.
The Zig Zag roughing option creates straight lines at a specified angle and contour moves at the boundaries.
-
Lesson #10: Roughing Outermost Shape as Boss
Available only when Use Stock is in effect. Applies to 2D geometry only. When this checkbox is selected, the system will regard remaining stock to be machined as a boss (rather than as a pocket with one or more air walls) and will therefore remove material outside the outermost loop.
Available only when Use Stock is in effect. Applies to 2D geometry only. When this checkbox is selected, the system will regard remaining stock to be machined as a boss (rather than as a pocket with one or more air walls) and will therefore remove material outside the outermost loop.
-
Lesson #11: Thread Milling
This function, in conjunction with a thread milling tool, lets you mill threads on the outer diameter (OD) or inner diameter (ID), clockwise (CW) or counterclockwise (CCW).
This function, in conjunction with a thread milling tool, lets you mill threads on the outer diameter (OD) or inner diameter (ID), clockwise (CW) or counterclockwise (CCW).
-
Lesson #12: VoluMill
The VoluMill function generates ultra high-performance toolpath in place of traditional roughing methods when the emphasis is on reducing cycle times, extending tool life, and reducing the stress on machine tools.
The VoluMill function generates ultra high-performance toolpath in place of traditional roughing methods when the emphasis is on reducing cycle times, extending tool life, and reducing the stress on machine tools.
-
Lesson #13: Toolpath Simulation
Toolpath simulation is the process of running a visual inspection of the operations you’ve created. Rendering steps through each operation, displaying the movement made by each tool as it cuts the part. This can be very helpful in catching any errors in the toolpath.
Toolpath simulation is the process of running a visual inspection of the operations you’ve created. Rendering steps through each operation, displaying the movement made by each tool as it cuts the part. This can be very helpful in catching any errors in the toolpath.
-
Lesson #14: Posting G-Code
Once the operations to machine the part have been created, the file needs to be post processed. Post processing converts a part file (VNC file) which contains the machining operations (toolpaths) into a text file (NC program) that can be transferred to the machine control. Post Processors specific to individual machine controls are used to convert the VNC file into a text file.
Once the operations to machine the part have been created, the file needs to be post processed. Post processing converts a part file (VNC file) which contains the machining operations (toolpaths) into a text file (NC program) that can be transferred to the machine control. Post Processors specific to individual machine controls are used to convert the VNC file into a text file.
-
Lesson #15: Part Duplication
In order to view part duplication, you need to select Op Sim Rendering. You can leave the Rendering palette open as you make your selections, rewind and play the simulation as required. Equally spaced, Grid, or Defined are selectable options.
In order to view part duplication, you need to select Op Sim Rendering. You can leave the Rendering palette open as you make your selections, rewind and play the simulation as required. Equally spaced, Grid, or Defined are selectable options.
-
Lesson #16: Custom Stock
For more complicated stock, the Workgroup context menu "WG Info" allows a custom stock shape definition from geometry. This dialog is accessed by right-clicking a workgroup’s name in the workgroup list.
For more complicated stock, the Workgroup context menu "WG Info" allows a custom stock shape definition from geometry. This dialog is accessed by right-clicking a workgroup’s name in the workgroup list.
-
-
-
Lesson #1: Creating Tools
To define turning tools, you must select a Lathe machine type in the DCD (Document Control Dialog). Basic turning tools are created using the Tool Creation dialog as featured in this video.
To define turning tools, you must select a Lathe machine type in the DCD (Document Control Dialog). Basic turning tools are created using the Tool Creation dialog as featured in this video.
-
Lesson #2: Holes
Holes Processes are used to make holes on center (X0). When the Holes Function tile is combined with a Tool tile, a hole process is created.
Holes Processes are used to make holes on center (X0). When the Holes Function tile is combined with a Tool tile, a hole process is created.
-
Lesson #3: DoIt vs ReDo
Defining when it is appropriate to select "DoIt" for an operation, versus "ReDo" for an operation, and the consequences of each selection.
Defining when it is appropriate to select "DoIt" for an operation, versus "ReDo" for an operation, and the consequences of each selection.
-
Lesson #4: Machining Markers
Machining Markers specify the start and end feature, and start and end point of the cut shape, the cut direction, and the offset position of the tool. These markers appear when you select geometry as the cut shape for Contouring and Roughing processes. The exception is when more than one set of geometry is selected. In this case, the system assumes that the cutting is on center or engraving.
Machining Markers specify the start and end feature, and start and end point of the cut shape, the cut direction, and the offset position of the tool. These markers appear when you select geometry as the cut shape for Contouring and Roughing processes. The exception is when more than one set of geometry is selected. In this case, the system assumes that the cutting is on center or engraving.
-
Lesson #5: Rough Turning
Rough turning processes are used to take multiple passes on a shape. When the Rough function tile is combined with a Tool tile, a roughing process is created.
Rough turning processes are used to take multiple passes on a shape. When the Rough function tile is combined with a Tool tile, a roughing process is created.
-
TEXT
-
Lesson #7: Contouring
The Contour process is used to take a single pass along a shape of circular cross-section. When the Contour Function tile is combined with a Tool tile, a process is created.
The Contour process is used to take a single pass along a shape of circular cross-section. When the Contour Function tile is combined with a Tool tile, a process is created.
-
Lesson #8: Threading
Lathe threading processes are used to create ID and OD threads. When the Threading Function tile is combined with a Tool tile, a threading process is created. There are three things the user must define in order to properly cut a thread using the system: what kind of thread to cut, how to cut the thread, and where to cut the thread.
Lathe threading processes are used to create ID and OD threads. When the Threading Function tile is combined with a Tool tile, a threading process is created. There are three things the user must define in order to properly cut a thread using the system: what kind of thread to cut, how to cut the thread, and where to cut the thread.
-
Lesson #9: VoluTurn
The VoluTurn process provides smooth flowing motion that evenly distributes wear on tool inserts and reduces machining loads by providing smooth circular tangential entry/exit, with efficient repositioning between cuts. VoluTurn is particularly well-suited to machining tough materials like titanium and hardened steels. It uses round inserts such as button inserts.
The VoluTurn process provides smooth flowing motion that evenly distributes wear on tool inserts and reduces machining loads by providing smooth circular tangential entry/exit, with efficient repositioning between cuts. VoluTurn is particularly well-suited to machining tough materials like titanium and hardened steels. It uses round inserts such as button inserts.
-
Lesson #10: Simulation
Op Sim, or Operation Simulation, is a rendering mode that allows users to visualize the toolpath of machining operations. It focuses on displaying the toolpath without showing material removal. - Part-Centric Display: Shows tool movements and paths for a single part. - Speed: Faster than Machine Simulation as it does not render an entire machine model. - Focus on Operations: Concentrates solely on individual operation details, excluding inter-operation moves.
Op Sim, or Operation Simulation, is a rendering mode that allows users to visualize the toolpath of machining operations. It focuses on displaying the toolpath without showing material removal. - Part-Centric Display: Shows tool movements and paths for a single part. - Speed: Faster than Machine Simulation as it does not render an entire machine model. - Focus on Operations: Concentrates solely on individual operation details, excluding inter-operation moves.
-
Lesson #11: Posting G-Code
Once the operations to machine the part have been created, the file needs to be post processed. Post processing converts a part file (VNC file) which contains the machining operations (toolpaths) into a text file (NC program) that can be transferred to the machine control.
Once the operations to machine the part have been created, the file needs to be post processed. Post processing converts a part file (VNC file) which contains the machining operations (toolpaths) into a text file (NC program) that can be transferred to the machine control.
-
Create custom stock shapes for lathe operations.
-
-
-
-
Lace cutting is designed to cut surfaces at a specified angle and width.
-
Lace cutting is designed to cut surfaces at a specified angle and width.
-
2 Curve Flow
The 2 Curve Flow option creates toolpath that runs along or between two selected pieces of geometry and a solid that you can use for the cut shape.
The 2 Curve Flow option creates toolpath that runs along or between two selected pieces of geometry and a solid that you can use for the cut shape.
-
Surface Flow
Surface Flow Cut machines the entire area of a selected face. As such, Surface Flow Cut is designed for machining single faces, and works best when machining simple chamfers and fillets.
Surface Flow Cut machines the entire area of a selected face. As such, Surface Flow Cut is designed for machining single faces, and works best when machining simple chamfers and fillets.
-
Intersections
This surfacing option creates toolpath on selected intersections (either edges or faces of solids and sheets). The Intersections process is not restricted by stock definitions and does not recognize fixtures but is a gouge-free process that avoids red constraint faces.
This surfacing option creates toolpath on selected intersections (either edges or faces of solids and sheets). The Intersections process is not restricted by stock definitions and does not recognize fixtures but is a gouge-free process that avoids red constraint faces.
-
Constraining Toolpaths
Constraint Faces Clearance: The tool maintains this distance from any constraint face.
Constraint Faces Tolerance: This is the tolerance for the Constraint Face Clearance. A tight tolerance means more precise toolpath at the cost of potential efficiency.
Constraint Faces Clearance: The tool maintains this distance from any constraint face.
Constraint Faces Tolerance: This is the tolerance for the Constraint Face Clearance. A tight tolerance means more precise toolpath at the cost of potential efficiency.
-
-
-
Surfs Tab
For the Advanced 3D Machining process, you use the Surfs. (Surfaces) tab to set basic information such as:
Type of cut. l Speeds and feeds. l Basic parameters including stock to leave, stepovers, and tolerances. l Settings such as Clearances, Cut Depth, and Plunging. l Options that are common to all processes. l Controls that are specific to the toolpath cut type you select.
For the Advanced 3D Machining process, you use the Surfs. (Surfaces) tab to set basic information such as:
Type of cut. l Speeds and feeds. l Basic parameters including stock to leave, stepovers, and tolerances. l Settings such as Clearances, Cut Depth, and Plunging. l Options that are common to all processes. l Controls that are specific to the toolpath cut type you select.
-
Options Tab
This tab provides options for the Advanced 3D toolpath type you are generating. For the most part, they are generic, with each toolpath cut type having slight differences in the options.
This tab provides options for the Advanced 3D toolpath type you are generating. For the most part, they are generic, with each toolpath cut type having slight differences in the options.
-
Entry/Exit Tab
The items found on this tab control the toolpath as it enters or leaves the surface to be cut.
The items found on this tab control the toolpath as it enters or leaves the surface to be cut.
-
Boundary Tab
Boundaries allows you to restrict the toolpath computation to the geometrical size of the model or to use pre-defined geometry as a boundary limitation.
Advanced 3D Machining processes are boundary based, meaning that each and every operation needs a boundary to be defined, even if it is just the default stock definition.
Boundaries allows you to restrict the toolpath computation to the geometrical size of the model or to use pre-defined geometry as a boundary limitation.
Advanced 3D Machining processes are boundary based, meaning that each and every operation needs a boundary to be defined, even if it is just the default stock definition.
-
Pocketing
You can use this cut type to clear large quantities of material very quickly, leaving only a minimal amount of remaining material. Some amount of remaining material is usually left behind for finish machining.
You can use this cut type to clear large quantities of material very quickly, leaving only a minimal amount of remaining material. Some amount of remaining material is usually left behind for finish machining.
-
Core Detection
This cut type is a variant of the standard Pocketing cut type, with a few controls that are different. Instead of values for minimum and maximum stepover (which govern each pass in a regular Pocketing cut type), you specify values for Rough Stepover and Cleanup Stepover, which govern separate passes.
This cut type is a variant of the standard Pocketing cut type, with a few controls that are different. Instead of values for minimum and maximum stepover (which govern each pass in a regular Pocketing cut type), you specify values for Rough Stepover and Cleanup Stepover, which govern separate passes.
-
Adaptive Pocketing
You can use this cut type to clear large quantities of material very quickly, leaving only a minimal amount of remaining material. Some amount of remaining material is usually left behind for finish machining. The toolpath produced by Adaptive Pocketing is different from regular pocketing in being longer but smoother, with fewer abrupt changes in tool direction or tool load.
You can use this cut type to clear large quantities of material very quickly, leaving only a minimal amount of remaining material. Some amount of remaining material is usually left behind for finish machining. The toolpath produced by Adaptive Pocketing is different from regular pocketing in being longer but smoother, with fewer abrupt changes in tool direction or tool load.
-
Lace Cut
Usually, you use the Lace Cut cut type to create a finishing operation. There are several different styles of lace cuts available.
Usually, you use the Lace Cut cut type to create a finishing operation. There are several different styles of lace cuts available.
-
N Curve Flow
This process creates toolpath where each pass is parallel or perpendicular to the selected curves. The toolpath morphs between the curves. This process accepts either two Drive Curves or any number of Drive Curves with two Trim Curves.
This process creates toolpath where each pass is parallel or perpendicular to the selected curves. The toolpath morphs between the curves. This process accepts either two Drive Curves or any number of Drive Curves with two Trim Curves.
-
Curve Projection
This process creates toolpath that projects a curve (a spline) onto the faces of a solid. The toolpath is just a single Z-step down but you may perform multiple offsets to widen the area machined.
This process creates toolpath that projects a curve (a spline) onto the faces of a solid. The toolpath is just a single Z-step down but you may perform multiple offsets to widen the area machined.
-
Contour
This process is typically used for semi-finishing or finishing passes and is sometimes referred toas “Waterline Machining” or “Constant Z Machining”. This process is best used on parts with vertical or near vertical walls. This is because the step down is calculated in the Z-axis and the results are better on vertical or near vertical areas. The material cannot be removed as effectively on horizontal areas which would normally be machined using a different strategy.
This process is typically used for semi-finishing or finishing passes and is sometimes referred toas “Waterline Machining” or “Constant Z Machining”. This process is best used on parts with vertical or near vertical walls. This is because the step down is calculated in the Z-axis and the results are better on vertical or near vertical areas. The material cannot be removed as effectively on horizontal areas which would normally be machined using a different strategy.
-
Constant Stepover
This process is typically used for semi-finishing or finishing passes and is sometimes referred toas “Waterline Machining” or “Constant Z Machining”. This process is best used on parts with vertical or near vertical walls. This is because the step down is calculated in the Z-axis and the results are better on vertical or near vertical areas. The material cannot be removed as effectively on horizontal areas which would normally be machined using a different strategy.
This process is typically used for semi-finishing or finishing passes and is sometimes referred toas “Waterline Machining” or “Constant Z Machining”. This process is best used on parts with vertical or near vertical walls. This is because the step down is calculated in the Z-axis and the results are better on vertical or near vertical areas. The material cannot be removed as effectively on horizontal areas which would normally be machined using a different strategy.
-
Flats Cut
This process type machines all of the flat areas of the selected faces. This process is often used for finishing a part where excess material has already been cleared. Flats Cut acts upon completely flat areas only.
This process type machines all of the flat areas of the selected faces. This process is often used for finishing a part where excess material has already been cleared. Flats Cut acts upon completely flat areas only.
-
Intersections Machining
This process type creates a single pass along all corners of the part. This process is intended to finish the part using pencil or rest milling after general machining of a component with a larger tool. The area to be machined is determined by the diameter of the tool selected.
This process type creates a single pass along all corners of the part. This process is intended to finish the part using pencil or rest milling after general machining of a component with a larger tool. The area to be machined is determined by the diameter of the tool selected.
-
Intersections Rest Machining
This process type creates toolpath that removes all the un-machined areas of a hypothetical previous tool. This is basically a pencil milling strategy calculated using a Reference Tool diameter. If there are radii on the model with values equal to or greater than the Reference Tool radius, these areas are not machined. This allows for fast toolpath calculation and good finishing.
This process type creates toolpath that removes all the un-machined areas of a hypothetical previous tool. This is basically a pencil milling strategy calculated using a Reference Tool diameter. If there are radii on the model with values equal to or greater than the Reference Tool radius, these areas are not machined. This allows for fast toolpath calculation and good finishing.
-
Steep Shallow
This process type creates toolpath that machines Steep areas and Shallow areas using different strategies. This is a “one-step” finishing routine. Very complex parts can be finished using just this process because you can define an angle that splits the Steep areas from the Shallow areas and thus define different machining strategies for each zone.
This process type creates toolpath that machines Steep areas and Shallow areas using different strategies. This is a “one-step” finishing routine. Very complex parts can be finished using just this process because you can define an angle that splits the Steep areas from the Shallow areas and thus define different machining strategies for each zone.
-
Toolpath Splitter
This process type is for splitting up very long toolpath. This is intended as a method to force a tool change, saving the cutter. To create this process type you must start with an Advanced 3D process.
This process type is for splitting up very long toolpath. This is intended as a method to force a tool change, saving the cutter. To create this process type you must start with an Advanced 3D process.
-
Toolholder Gouge Check
This process type splits up the toolpath of another process type. The toolpath is split based upon where the tool and its holder can fit. To create this process type, you must start with an Advanced 3D process.
This process type splits up the toolpath of another process type. The toolpath is split based upon where the tool and its holder can fit. To create this process type, you must start with an Advanced 3D process.
-
Text.
-
-
-
Operation Tile Stacking
GibbsCAM's operations list offers four choices for organizing op tiles: Individual, Process Mode, Process List, & Manual.
GibbsCAM's operations list offers four choices for organizing op tiles: Individual, Process Mode, Process List, & Manual.
-
Bulk CS & WG Management
The context menus (right-mouse menus) of the WG (Work Group) and CS (Coordinate System) dialog boxes have new items making it easier to handle workgroups and coordinate systems.
The context menus (right-mouse menus) of the WG (Work Group) and CS (Coordinate System) dialog boxes have new items making it easier to handle workgroups and coordinate systems.
-
Fillet-Chamfer
Geometry Fillet-Chamfer dialog now provides a Multiple Circle button, for rapidly filleting or chamfering selections of differing radii.
Geometry Fillet-Chamfer dialog now provides a Multiple Circle button, for rapidly filleting or chamfering selections of differing radii.
-
Built-in G-Code Editor
GibbsCAM features a fully functioning g-code editor, built directly into the posting dialog!
GibbsCAM features a fully functioning g-code editor, built directly into the posting dialog!
-
Advanced Entry & Exit
THIS FEATURE ROCKS! GibbsCAM CAD/CAM Software lets you specify a custom path for tool approach and retract. Determine exact tool locations to avoid interference between tool & stock for such operations as back boring, milling with angled heads, and ID or OD turning.
THIS FEATURE ROCKS! GibbsCAM CAD/CAM Software lets you specify a custom path for tool approach and retract. Determine exact tool locations to avoid interference between tool & stock for such operations as back boring, milling with angled heads, and ID or OD turning.
-
Clearance Volumes
Ready to terrify your operators? GibbsCAM CAD/CAM Software Clearance Volume determines efficient clearances for interop moves when the tool retracts to accommodate rotation.
Ready to terrify your operators? GibbsCAM CAD/CAM Software Clearance Volume determines efficient clearances for interop moves when the tool retracts to accommodate rotation.
-
Automatic Deburring
Tired of benching parts? GibbsCAM CAD CAM Software 5-Axis Deburring provides automatic feature detection, automatic linking, automatic lead in, and automatic collision avoidance, creating toolpath in a completely automated fashion just by selecting the part geometry.
Tired of benching parts? GibbsCAM CAD CAM Software 5-Axis Deburring provides automatic feature detection, automatic linking, automatic lead in, and automatic collision avoidance, creating toolpath in a completely automated fashion just by selecting the part geometry.
-
Milling Chamfers & Tapers
GibbsCAM makes milling chamfers & tapers powerfully simple. Here's a quick explainer.
GibbsCAM makes milling chamfers & tapers powerfully simple. Here's a quick explainer.
-
Pinch Turning
Pinch Turning with GibbsCAM is powerfully simple. We are the leaders for Multi-Task Machine (MTM) programming!
Pinch Turning with GibbsCAM is powerfully simple. We are the leaders for Multi-Task Machine (MTM) programming!
-
Drilling to depth via the tip or diameter of your drill is easy as pie with GibbsCAM.
-
Solid Model Interrogation
Need quick & easy data from a solid model? GibbsCAM's solid model interrogation ability is simply powerful. Alt+Click on a surface, and the values auto-fill.
Need quick & easy data from a solid model? GibbsCAM's solid model interrogation ability is simply powerful. Alt+Click on a surface, and the values auto-fill.
-
Threadmilling
Learn how to thread mill within GibbsCAM. Full profile threadmilling allows for multiple teeth and provides support for thread forms and tapered-angle tools. Support for tapered threads using single and multi-point thread tools, including NPT and BSPT types. Multiple passes and spring passes, providing optimal thread finish are also supported.
Learn how to thread mill within GibbsCAM. Full profile threadmilling allows for multiple teeth and provides support for thread forms and tapered-angle tools. Support for tapered threads using single and multi-point thread tools, including NPT and BSPT types. Multiple passes and spring passes, providing optimal thread finish are also supported.
-
MDD & VMM Files
Ever wonder where to put those MDD & VMM files you received from us? It's easier than you ever imagined!
Ever wonder where to put those MDD & VMM files you received from us? It's easier than you ever imagined!
-
See the many ways you can find your cycle time within GibbsCAM.
-
Creating, saving, & loading tool lists within GibbsCAM.
-
Positioning Solid Models
See how to quickly & easily orient your solid model for machining. We cover both mill and lathe parts.
See how to quickly & easily orient your solid model for machining. We cover both mill and lathe parts.
-
Volumetric Turning
VoluTurn is a powerful new toolpath technology that can significantly improve the machining of any part that is turned using round inserts and offers manufacturers the ability to significantly increase productivity by reducing cycle times while also reducing wear on cutting tools.
VoluTurn is a powerful new toolpath technology that can significantly improve the machining of any part that is turned using round inserts and offers manufacturers the ability to significantly increase productivity by reducing cycle times while also reducing wear on cutting tools.
-
Double Milling
Take your multi-turret lathe to the next level with our new double milling capabilities.
Take your multi-turret lathe to the next level with our new double milling capabilities.
-
Installing Post, MDD, & VMM Files
Where should you be installing your GibbsCAM Post processors, MDDs, & VMMs?
Where should you be installing your GibbsCAM Post processors, MDDs, & VMMs?
-
Freehand Toolpath
Create your own freehand toolpath within GibbsCAM, the ultimate in CNC program customization!
Create your own freehand toolpath within GibbsCAM, the ultimate in CNC program customization!
-
Duplicate Toolpaths & Patterns
The Pattern checkbox is available for all 2D and 2½D milling processes and for Advanced 3D. It allows the toolpath generated by the process to be duplicated in different locations on the part. Using Pattern will create subprograms in the post file to make the code more efficient.
The Pattern checkbox is available for all 2D and 2½D milling processes and for Advanced 3D. It allows the toolpath generated by the process to be duplicated in different locations on the part. Using Pattern will create subprograms in the post file to make the code more efficient.
-
Solid Model Visibility & Clean-up
Tips for clarifying & simplifying CAD models upon importing them into GibbsCAM.
Tips for clarifying & simplifying CAD models upon importing them into GibbsCAM.
-
Transform Toolpath
Take any toolpath operation and duplicate it without modifying your geometry or solid model.
Take any toolpath operation and duplicate it without modifying your geometry or solid model.
-
Unstitch & Offset
Learn more about these powerful tools for the creation & programming of solid models.
Learn more about these powerful tools for the creation & programming of solid models.
-
Learn best practices, and how to leverage solid model history within GibbsCAM.
-
Solids Light
This basic upgrade available for all 2D users, allows the import, creation, and machining of solid models.
This basic upgrade available for all 2D users, allows the import, creation, and machining of solid models.
-
MEET YOUR INSTRUCTORS
Dave McCray
GibbsCAM professional since 1992
40+ years CNC machining experience
One of the most experienced CAD/CAM guys in the nation, Dave is an invaluable asset to all our customers. Dave handles customer training, technical support, and post modification.
Bill Reed
GibbsCAM professional since 2000
30+ years CNC machining experience
As a machinist and programmer for over 30 years, Bill has been a GibbsCAM user for over 23 years while also working in Machine Tool Applications and Cutting Tool Sales. With a background in Medical and Aerospace manufacturing.